Il y a presque 30 ans environ, j’ai eu l’opportunité d’animer une démarche d’amélioration Qualité au sein de l’entreprise dans laquelle j’exerçais. La méthode utilisée s’appelait à cette époque « Cercle de Qualité », datait des années 60, provenait…du japon et était initiée par Kaoru Ishikawa dont le diagramme « en arêtes de poisson » a depuis fait le tour du monde. La base du Kaisen des temps modernes.
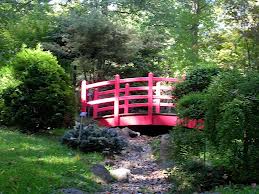
En synthèse, chaque acteur dans la chaîne de production qu’il soit côté « ateliers » ou « administratif » devait identifier et hiérarchiser les anomalies, prendre en compte l’impact de la non qualité dans le processus, réfléchir aux solutions applicables, initier leurs mises en oeuvre et mesurer la performance en terme d’amélioration, pour éventuellement ajuster les procédures, etc.
Depuis ces années, très régulièrement sont apparues sur le marché des méthodes qui n’apportaient selon moi que de simples évolutions dans la démarche originelle de Kaoru Ishikawa et n’avaient, finalement et en synthèse, de fondamentalement nouveau que le nom.
Aujourd’hui, out les cercles de qualité !
Le marketing a rebaptisé la démarche d’un terme anglophone, bien plus vendeur.
Pour ne pas être « hasbeen », il faut, pour la démarche Qualité, aujourd’hui employer le terme LEAN : Lean Manufacturing, Lean Office, Lean IT, etc. Auquel on peut adjoindre les termes Six Sigma, White Belt, Black Belt, Business Process Management, etc pour ce qui concerne le côté méthode.
L’objectif reste le même :
– Amélioration qualité des produits et services
– Meilleure fluidité des informations dans leur acheminement
– Meilleure réactivité et autonomie des équipes
Pour pouvoir améliorer un processus, encore faut-il l’avoir identifié et compris.
Pour ce faire, chaque tâche qui compose le processus est alors inventoriée et son temps de réalisation (Lead Time) est évalué.
L’ensemble des tâches est hiérarchisé selon la chronologie des opérations.
La matrice SIPOC permet d’identifier les fournisseurs du processus (externes ou internes), les entrées complémentaires, le process, les éléments de sortie et le client (externes ou internes) qui hérite des résultats du processus.
Les méthodes VSM (Value Stream Mapping) ou MIFA ( Material and Information Flow Analysis) permettent de modéliser les processus à l’aide d’outils comme Microsoft Visio, Dia en open source ou Gliffy en Saas.
Le tout compose alors la cartographie du procédé.
Une fois les processus modélisés, reste à les améliorer ou les optimiser.
La méthode QQOQCCP (pour « Qui ? Quoi ? Où ? Quand ? Comment ? Combien ? Pourquoi ? »), ou 5W en anglais (pour « Who, What, Where, When, Why ? ») aide à se poser l’ensemble des questions relatives à un point et évite d’oublier une dimension du problème à traiter.
Le principe de Pareto va aider à hiérarchiser les thématiques à aborder selon le constat que 80 % des effets sont le produit de 20 % des causes.
Pour la recherche de solution, la méthode des 5S permet d’appliquer une démarche logique d’amélioration :
Seiri : Supprimer tout ce qui ne sert à rien ou le rendre disponible ponctuellement plutôt que de manière permanente.
Seiton : Situer les équipements et les outils, ranger son espace de travail
Seiso : Scintiller pour la phase de nettoyage
Seiketsu : Standardiser la procédure précédente pour la rendre permanente.
Shitsuke : Suivre l’application de la procédure
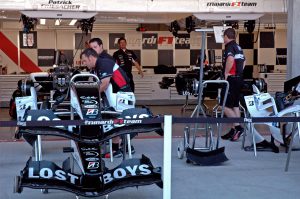
Chaque plan d’action correctif suivra la logique d’amélioration continue de la roue de Deming PDCA,
Plan : Planification des travaux
Do : Exécution des travaux
Check : Contrôle qualité des travaux
Act : Correction des dérives.
ou de la variante Six Sigma DMAIC.
Défine : Définition de l’objectif
Measure : Mesure, collecte d’indicateurs qui fournissent les quantités
Analyse : Recherche des causes des problèmes
Improve : Quelles sont les solutions pour respecter l’objectif
Control : Vérification à travers les mesures que le plan d’action respecte l’objectif.
La démarche d’amélioration des processus de travail a d’abord été initiée au sein des ateliers de fabrication et se décline aujourd’hui dans sa version Lean Manufacturing.
Depuis, crise aidant, la recherche de gains de productivité a conquis les fonctions administratives et services généraux sous la forme du Lean Office.
Le Lean IT est, quant à lui, la déclinaison de cette démarche d’amélioration contextualisée aux services informatiques et DSI dans leurs fonctions d’étude, de production et de support.
Lean à tous les étages !